Tensile, Impact, and Hardness Testing—What Each Tells Us About a Metal’s Behavior
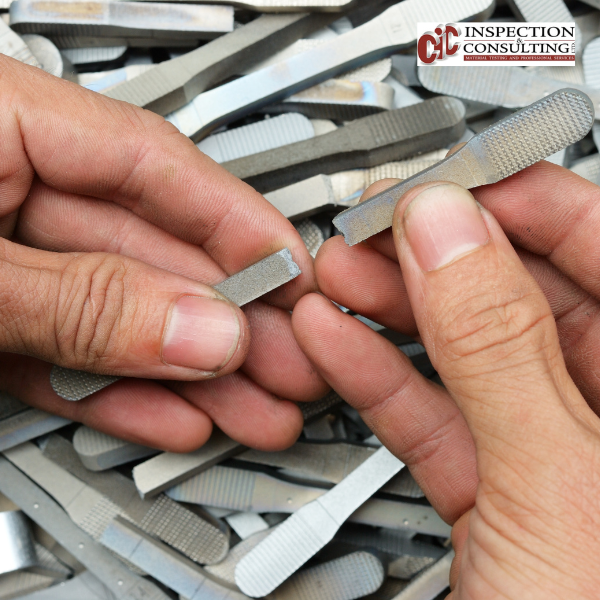
In industries that rely on metals—from structural steel fabrication to pressure vessel manufacturing and heavy equipment production—understanding how a material will behave under stress isn’t a luxury; it’s a necessity. Engineers, metallurgists, and quality assurance professionals depend on a range of mechanical tests to ensure that the materials used in critical components will perform as expected under load, impact, and time. Among these, tensile, impact, and hardness testing stand as the three pillars of material evaluation.
While they may sound similar, each of these tests uncovers different characteristics of a metal’s behavior. Together, they provide a full-spectrum picture of a material’s strength, ductility, toughness, and resistance to deformation. Skipping any one of them can leave blind spots—sometimes with costly or catastrophic consequences.
Let’s break down what each test tells us, and why all three are essential in quality control, failure analysis, and material selection.
Tensile Testing: How Much Can It Take Before It Breaks?
Tensile testing is the most fundamental and widely used mechanical test for metals. It involves stretching a specimen under controlled tension until it fractures. The test reveals key data points such as yield strength, ultimate tensile strength (UTS), elongation, and reduction of area.
Yield strength tells you the stress point at which a material begins to deform plastically—permanently. This is crucial for load-bearing applications like beams, fasteners, and pressure components. The UTS measures the maximum stress the metal can withstand, while elongation shows how much a material can stretch before breaking—an indicator of ductility.
In practical terms, tensile testing answers questions like: Will this component deform under load? Will it snap under tension? Can it bend without failing? Whether you're designing a bridge, a boiler, or a crane hook, these answers matter.
Impact Testing: Will It Survive a Sudden Blow?
Impact testing, particularly the Charpy V-Notch test, assesses how much energy a material can absorb during a high-velocity impact. A notched specimen is struck by a swinging pendulum, and the energy absorbed during fracture is recorded.
This test is vital for understanding toughness, especially in applications exposed to sudden or dynamic loading—think mining equipment, pipeline welds, offshore structures, or winter-weather steel components. It’s not just about how strong the material is, but how well it can resist cracking or catastrophic failure when hit hard or suddenly.
In Canadian standards, especially in applications governed by CSA W47.1/W59 or pressure vessel codes like ASME Section VIII, impact testing is mandatory in certain service conditions—particularly at low temperatures. Steel that performs well in summer may become brittle and fail in sub-zero temperatures unless it passes proper impact testing.
Hardness Testing: How Resistant Is It to Wear and Indentation?
Hardness testing measures a metal’s resistance to surface deformation, typically from penetration or scratching. Common methods include Brinell, Rockwell, and Vickers testing, each suited to different material types and applications.
The results offer a quick and reliable indicator of wear resistance, heat treatment effectiveness, and material consistency across a batch. In components like gears, shafts, and hardened bushings—where surface integrity is key—hardness data helps confirm that the metal will perform under repeated contact, pressure, or abrasion.
It’s also an essential quality control step for verifying heat treatment processes. A metal that’s too hard may be brittle; too soft, and it may deform or wear prematurely. Hardness testing strikes the balance, often serving as a fast field method to confirm proper material condition without the need for destructive testing.
Why All Three Matter
These tests don’t exist in silos. A material that scores high in tensile strength but low in impact toughness may be strong but dangerously brittle. Likewise, high hardness may suggest surface strength but reveal nothing about how a component will behave under tensile loads or rapid impact.
That’s why, in real-world applications, engineers rely on a combination of tensile, impact, and hardness data to make informed decisions. Whether you’re qualifying materials for welding, verifying vendor-supplied steel, or conducting failure analysis after a component break, these tests provide the hard evidence needed to move forward confidently.
A Final Thought on Testing Strategy
In an era of increasingly advanced materials and ever-tightening performance expectations, understanding what each test reveals isn’t just for lab technicians—it’s strategic insight for anyone involved in design, construction, or quality assurance.
Without testing, you're guessing. And when it comes to critical infrastructure or high-risk industrial applications, guesswork is not an option.